Ideally, supply chains are designed to flow seamlessly. The journey that products take as they travel from their raw material state to the end user’s hands is supposed to function like clockwork.
Fortunately, there are steps you can take to fortify your organization and maintain manufacturing success, even amid supply chain disruption.
8 Tips for Navigating Supply Chain Disruption
1. Improve Supply Chain Visibility
The only way to successfully survive a supply chain disruption is to maintain a supplier network and keep parts and materials steadily flowing. This is why transparency and visibility are key.
New and Innovative Ways of Working
Improve your processes to increase revenue, cut operational costs and drive competitive advantage.
One way to achieve visibility is by using supply mapping to help executives better understand how their supply chain works.
For example, where is each plant located and what does it manufacture? Moreover, which parts are critical, and which can use alternatives? Which parts can you source from somewhere else?
Insights into each plant’s operational status and inventory requirements are also critical.
To provide all of this data and more, an ERP implementation may be necessary. Providing up-to-the-minute inventory management, an ERP solution can provide ERP business intelligence that helps you anticipate issues before they occur.
To learn more about how companies are using ERP software for supply chain management, read our blog post, What is ERP in Supply Chain Management?
2. Increase Internal Collaboration
If your teams are operating in silos, it will be that much more difficult to weather the storm of a supply chain disruption. Especially in the middle of a crisis, internal collaboration is essential.
For example, your customer service department should have a direct line to your sales team, who should know exactly how to reach your project managers.
When key stakeholders are involved and working with one another, conflicts are avoided and strategic relationships are fostered.
Business technology solutions, like ERP systems, can facilitate cross-functional workforce communication and ensure that everyone is working from the same dataset. This way, your teams can work together to identify trends, forecast future issues and prevent problems.
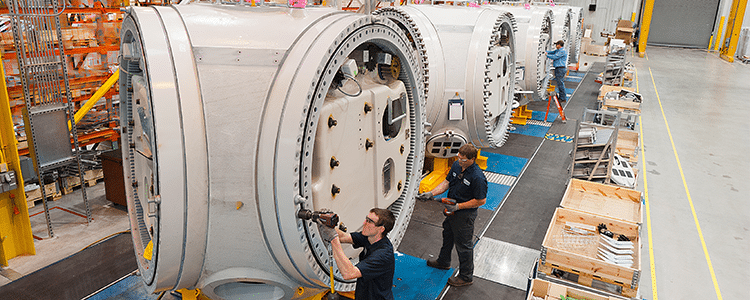
3. Predict Demand
A crisis can render demand unpredictable, making it imperative to keep a close eye on demand at all times.
As you track and analyze demand, pay close attention to current trends and consumer behavior. Are frantic shoppers stampeding toward the toilet paper aisle or hoarding mounds of paper towels? By analyzing demand, you can adjust inventory levels as necessary in response to those shifts.
While an increase in demand may be benefiting some retailers’ bottom lines, it is placing a strain on manufacturers who are not prepared to meet last-minute requests. This is especially the case in health care manufacturing, where demand for face masks is climbing by the day, and U.S.-based manufacturers simply can’t keep pace.
In contrast, other industries are figuring out how to navigate a decrease in demand. For example, many car manufacturers are now manufacturing ventilators to make up for the decrease in demand for cars (and to help save lives).
Car manufacturers’ ability to adapt quickly was enabled by demand forecasting. In addition, they likely are relying on flexible ERP software with functionality supporting a variety of manufacturing requirements.
While these demand shifts will eventually normalize, other factors in the future will inevitably impact demand. As such, we recommend developing a contingency plan that clearly describes how you’ll handle a change in demand. This way, when it happens, you won’t be caught off-guard.
Along with a change in demand often comes an increase in customer support requests. You can stay ahead of this by evaluating your IT infrastructure and improving your customer support processes.
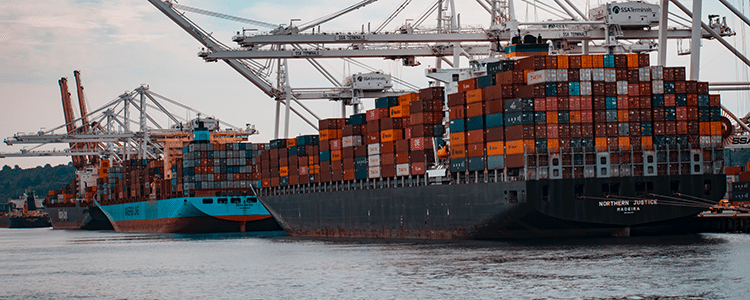
4. Enlist New Suppliers
Does your company depend on a network of suppliers in various locations around the world? In global supply chains like this, disruptions are expected, and often linked to situations outside your control.
To mitigate risk, be wary about relying completely on single-source suppliers. You should always have a backup resource, wherever possible, to ensure you can stay in business whenever chaos strikes.
While this helps ensure supply chain stabilization and resilience, it can come at a price. Utilizing new suppliers and alternative means of outsourcing isn’t always cost-effective, but it can be the most viable option in some cases.
5. Invest in Omnichannel Distribution
How does your company currently allow users to purchase and receive your products? If you rely solely on brick-and-mortar foot traffic, the coronavirus crisis is likely hitting your business harder than others.
If your store doesn’t have an e-commerce presence, that could mean missing out on a ton of potential revenue. It could also render your infrastructure more susceptible to defeat whenever a major disruption drastically changes consumer behavior.
To adapt to the needs of consumers’ needs today, many brick-and-mortar restaurants have added an online menu of to-go meals or grocery items to their menus, all to figure out a way to simply survive.
One of the pillars of successful supply chain management is varying your distribution methods across both physical and digital platforms. If this isn’t already true of your business, you may need to develop a new IT digital strategy.
6. Try to Retain Your Workforce
As companies around the world adjust to the new normal, unemployment is growing at an unprecedented rate. However, cutting your staff down to the bare minimum isn’t always the best option.
This is the time to focus on workforce retention. When your supply chain is in crisis mode, you’ll need people in place who know what they’re doing.
In addition, certain employees may be necessary for enabling you to change your business model. Remember the restaurants offering to-go menus? Some waitstaff have added “delivery driver” to their resumes to ensure that they still have a job and remain essential.
Rather than scrimping on workforce protections, we recommend continuing to invest in employees, and if necessary, hiring a human capital management consultant. This will put you in a better position for recovery down the road.
For those of you planning to retain your workforce, we have outlined a variety of alternatives to layoffs in one of our recent blog posts.
7. Perform Financial Stress Testing
Once relegated primarily to the banking realm, financial stress testing is a beneficial risk measurement exercise for any company to perform.
It centers on quantifying your business risks in the context of both specific events and continuous scenarios. For example, there are myriad standards and regulations that help govern the supply chain industry. What would happen if you were found in non-compliance?
Model what both kinds of risk would look like for your organization, and model your response, too. Then, discuss with stakeholders what steps you will take to mitigate and respond.
8. Increase Customer Engagement
Customer engagement cannot fall by the wayside, even when your supply chain control mechanisms are turned upside down. Remember: Customers are the reason you’re in business.
Consistent communication is key. This is the time to ensure your brand is active on social media and maintaining an ongoing conversation with followers. It’s also important to post informative blogs, hold promotions, offer discount codes and ask relevant questions to build buzz.
A company with a satisfied and engaged customer base is inherently more stable, even when a situation happens that is beyond its control. As such, you may want to consider investing in customer experience transformation.
Successfully Navigating Supply Chain Disruption
A global crisis can trigger a supply chain disruption that affects even the most stable company. Yet, this setback doesn’t have to usurp all your manufacturing efforts.
When you’re prepared for such an event and have steps in place to work through it, you can emerge stronger than ever before. The key is thinking beyond the short-term effects of disruption and considering how this challenge will affect your business in the long term.
Sometimes, a disruption is the jolt that companies need to finally make tough but necessary business decisions. We’re here to help you navigate these decisions. Request a free consultation below to discuss business process reengineering or ERP selection with one of our ERP consultants and business transformation experts.