Before you begin ERP selection, it’s important to conduct business process management. This will help you map your processes and determine your ERP requirements. It will also help you improve and standardize your processes. However, many business process management initiatives related to ERP implementations fail to result in measurable business benefits.
If you’re planning on conducting business process management or business process reengineering, there are several pitfalls to avoid along the way. Today, we’re sharing the top reasons why a business process management failure might occur and how you can avoid these missteps.
5 Reasons for Business Process Management Failure
1. Not Focusing on Standardization
An ERP system can provide visibility into your company’s core business processes, but it can’t live up to this expectation when your processes are scattered and inconsistent.
If your business spans multiple locations, it’s natural to have some degree of variation. For instance, different locations may have slightly different shipping processes. However, it’s important to standardize where possible. This helps ensure a seamless workflow throughout your enterprise and improves collaboration and communication between team members.
When determining whether to standardize a particular process, it helps to consider the “why” behind the process. Is it done this way because it’s always been done this way, or is there a compelling business reason?
ERP Selection Case Study
We helped this manufacuturer select a modern ERP system to keep pace with its rapid growth.
2. Automating Inefficient Processes
While ERP software allows your organization to automate some of your most manual, time-consuming tasks, this technology is rendered ineffective if you use it to automate business processes that are inefficient.
Many companies rush through business process management, eager to start implementation. They map their current state, determine their ERP requirements and then hand these requirements to the ERP vendor.
Sadly, this approach can be a costly and resource-draining mistake. You’ll end up needing to improve your processes after implementation when it will be much more complex and expensive.
We recommend taking the time to improve your processes early so vendors know what functionality you really need. Process improvement is a separate conversation than process standardization but it’s just as important to do it early.
3. Lack of Employee Involvement
Is your ERP project team operating in a silo? If you’re forging ahead without requesting the involvement and input of your employees, you could miss more than a few inefficiencies.
Your employees are the ones most qualified to speak to which business processes are working and which are not. That’s why it’s important to involve employees from across departments in process mapping. They have a working knowledge of the pain points that currently exist and can offer valuable insights into how to these pain points should be addressed.
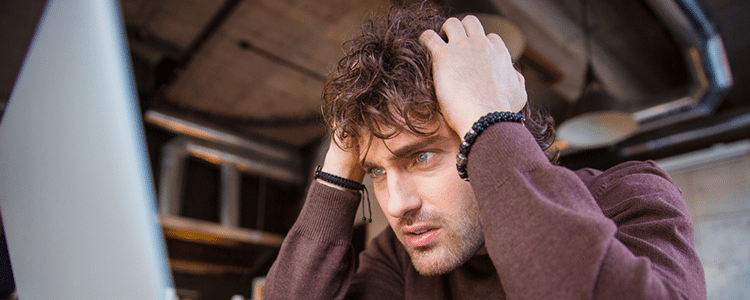
4. Lack of Executive Buy-in
Executive buy-in and support is just as important as employee participation. If your C-suite isn’t involved in process improvement efforts, then it will become apparent after go-live when you find that the system doesn’t support overarching business goals.
Executive involvement means the C-suite is allocating sufficient budget and resources to business process management because your executives support the project vision. It also means the C-suite is available for ad hoc meetings when it’s time to make important process decisions.
5. Lack of Organizational Change Management
Of course, any time you change a business process, you open your company up to dissent and confusion. This is especially the case if you alter or completely do away with “tried-and-true” business processes.
This is where effective organizational change management is a must. Simply throwing the new processes at the wall and hoping they stick is bound to amplify any brewing frustrations.
Instead, communication should come from the top, and should begin as early as possible. Leaders should be equipped to clearly communicate anticipated changes to employees, sharing key details including:
- Why the company is changing
- Why the change is happening now
- Exactly what processes will be changing
- What will stay the same
- The risks incurred if the company does not embrace the change
When this information is freely shared, it can help ease employees’ concerns and set the stage for a high rate of user adoption once the ERP solution goes live.
Avoid a Business Process Management Failure
While an ERP system can add efficiency and visibility to your processes, it’s important to make certain process improvements before implementation. We recommend focusing on the improvements that are expected to bring the most value with the least amount of effort.
A business process management failure is avoidable if you know the right methodology and partner with the right team of ERP consultants. Our team is here to help you every step of the way, so request a free consultation below.