In 2011, grocery store chain Lidl kicked off what was meant to be a transformative initiative. Thousands of staff members and hundreds of outside consultants came together to help the German discount supermarket implement an enterprise resource planning (ERP) solution. With industry giant SAP at the helm, they initiated a project nicknamed “eLWIS,” an acronym for electronic Lidl merchandise management and information system.
The project continued for seven years, with SAP even recognizing Lidl as one of their top customers in 2017. However, by 2018, the ?Lidl ERP system and sap implementation failure was in full effect, costing the chain around 500M Euros, or $580 million USD, in total losses from this project.
What happened to cause this change of events? More importantly, what can your organization do to avoid such a setback in your own ERP implementation? In this case study, our ERP expert witnesses analyze the notable Lidl ERP system and SAP implementation failure.
4 Lessons Learned From the Lidl ERP Failure
1. Be Open to Business Process Reengineering
After the SAP ERP system failure, Lidl was forced to revert to its original inventory management system, with little to show for the project other than a major hit to its reputation and bottom line.
While there were many issues that ultimately led to the Lidl ERP system failure, there was one major challenge that held up progress from the very beginning. Put simply, Lidl was unwilling to change any of its business processes to fit the ERP vendor’s best practices.
Since its inception, Lidl has always based its inventory management on purchase prices, while the SAP platform is built on retail prices. Firmly against accepting this new approach, Lidl instead decided to customize the ERP software.
The only problem? The requirements gap was massive and trying to bridge it signaled the beginning of the end for this ill-fated project.
A requirements gap refers to the difference between the way your company wants to do something, and the way the ERP software is designed to perform that particular task. As expected, a smaller requirements gap means you need less customization, which results in an easier and less costly implementation.
By prioritizing business process improvement or business process reengineering, you can understand what’s currently working and what processes you need to change to make the best use of your new system. A willingness to look at requirements gaps and fix them at the onset can make all the difference between a project that stays on track and one that veers off course.
Contemplating litigation?
We are called upon to investigate the feasibility of litigation, provide software expert witness testimony and build background reporting for some of the industry’s highest-profile ERP lawsuits.
2. Adhere to a Defined Timeline When Possible
In all, the Lidl ERP project spanned around seven years. This is far longer than Lidl expected, and far longer than the business could withstand, considering that its retail and distribution needs were still very real – the pace of competition didn’t slow and neither did customer and partner expectations.
Trying to balance outside pressures with internal demands can cause an already-dragging project to slow down even more. In this case, the overwhelming number of customizations that the project required was the primary culprit behind the lagging schedule. This is yet another reason why it’s best to avoid extensive customizations and instead, leverage the best practices that most modern ERP systems provide.
3. Ensure Executive Alignment
Throughout the seven-year project, the Lidl executive team was in constant fluctuation. As leaders joined and exited the team, maintaining business-IT alignment and buy-in became more difficult.
We recommend aligning your executive team with project priorities. Otherwise, you will lack the resources, budget and focus you require.
In the case of Lidl’s project, it’s likely that the project lost momentum as the office door continued to revolve. New teams bring new priorities and goals, and it can be nearly impossible to keep a years-long initiative at the top of that list.
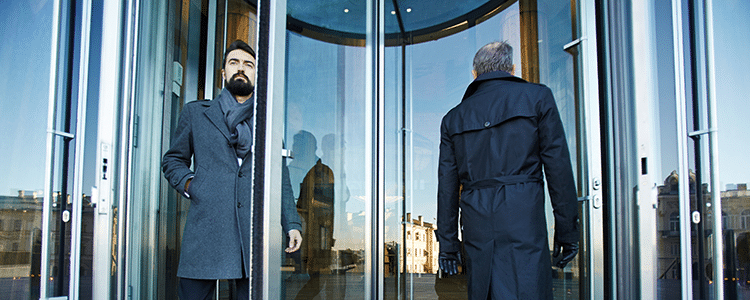
4. Prioritize Organizational Change Management
There wasn’t an inherent error or flaw in SAP’s ERP platform that caused the Lidl project to fail. In fact, SAP is an industry powerhouse. Recognized by Forbes as one of the top 25 most valuable brands in the world, its ERP solutions are among some of the most popular across business sectors.
Rather, the critical issue that lead to failure with this SAP ERP project was that Lidl unable to effectively prepare their workforce to make smart use of the software’s functionality.
While this sounds like an issue that could easily be avoided, the reality is that it’s all too easy for employees to hold tight to tried-and-true practices. This is where organizational change management comes into play. This is the structured process of looking at the “people side” of a major, enterprise-wide change. From managing resistance to communicating key messages, the steps your company takes to prepare employees before and during the ERP implementation directly affect the project’s outcome.
Learn From the Lidl ERP System Failure and Avoid Similar Setbacks
Any time a highly anticipated project fails, it can be devastating to the company involved. Factor in a loss of $580 million, and that’s one difficult lesson to learn.
The Lidl ERP system and SAP implementation failure might be in the past, but the project’s effects are still widely felt throughout the organization.
While the financial setback might be minimal compared to the annual revenue that the chain brings in, the company is still left with an outdated inventory management approach in dire need of modernization. Moving forward, this could directly affect the brand’s longevity and competitiveness in the market.
Your business might be in a different industry, but the lessons learned here are the same. To find out how you can apply these lessons to your project, contact our ERP consultants by requesting a free consultation below.