Continuous improvement is the persistent effort to make the best use of the systems or processes your company uses. Sometimes, these improvements happen all at once. Other times, they’re more incremental.
In either case, the progression is linear, and the goal is the same: fortifying and perfecting the aspects of your company that add value. At the same time, you’re working to eliminate aspects that are wasteful or non-value-adding.
Today, we’re sharing a few of the main benefits of continuous improvement. We’ll also explain what it entails – in general and also as it relates to ERP implementations.
Watch our video below or continue reading to learn more.
How Does Continuous Improvement Relate to ERP?
It is during the continuous improvement process that many companies realize their legacy systems aren’t up to speed. In other words, they find major inefficiencies and pain points in their operations that could be mitigated with a robust ERP system.
Continuous improvement is also relevant after an ERP implementation. Post go-live continuous improvement is about looking for opportunities to keep improving the new ERP system and processes. Building an ERP center of excellence is essential in this effort.
5 Benefits of Continuous Improvement
With so much on your plate already, why should you prioritize continuous improvement? Let’s take a look at a few of the top reasons you should invest in this effort, whether or not you’ve implemented ERP software.
1. Improved Employee Morale
Continuous improvement isn’t a siloed activity isolated to a few individual teams. Rather, it’s an initiative that permeates your entire company culture, wherein every employee is dedicated to making the best use of the tools they’re given.
In turn, this can help encourage a more active and involved workforce, where everyone feels that they’re an important and valued part of company goals. This can bolster employee morale, lower employee turnover and help drive increased user adoption for any new technology.
The 2025 ERP Report
72.6% of respondents said they've already deployed AI at their organizations. Learn about AI adoption and other ERP trends by downloading our latest report.
2. Improved Product Quality
If you’re continuously focused on improving your products, services and processes, it’s inevitable that you’ll also drive improved quality across the board. This effort requires you to take a close and careful look at your operations, identifying any problems that could compromise the final output.
Even if everything is going very well, there are always opportunities to make them better. With continuous improvement, you can hold your teams accountable to higher levels of quality, fine-tuning every aspect on the path to innovation.
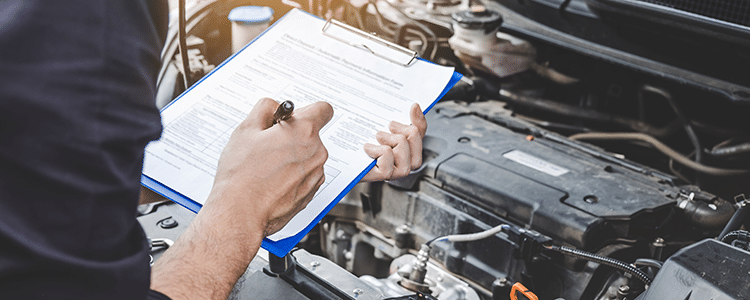
3. Increased Efficiency
It’s likely that your company has been following the same general procedures and workflows for years. If this is the case, you could be stuck in a rut and not even realize it. Without analyzing ways to improve, you could remain at the same efficiency level while failing to realize there’s an easier, better and more profitable way to get the job done.
Continuous improvement means looking for ways to work smarter, not harder, so you can perform tasks in a fraction of the time without compromising quality.
Many times, this requires business process reengineering, which goes beyond process improvement and instead focuses on redesigning existing processes. The goal is to build revenue, cut operational costs and drive competitive advantage. This can translate into reduced lead and processing times and faster deliveries, among other benefits.
4. Lower Costs
How much money is your company currently spending on technology or processes that do not add value? Chances are that this number is higher than you think.
One of the driving principles of lean management is looking for areas of waste. Once those areas are found, you can eliminate them altogether or alter them to become less resource-draining.
While this is an obvious benefit in manufacturing, it can also help many other industries tighten their controls and improve their standing.
Consider financial institutions, for instance. An advising firm might currently charge fees to account for the overhead it has to carry, but if it can remove internal waste, it may be able to eliminate or lower these fees to improve its competitive position.
5. Improved Customer Satisfaction
At the outset, it might seem like continuous improvement is strictly an in-house effort. While a majority of the tasks do center on internal optimization, they flow directly into your customer-facing operations.
Higher-quality products mean fewer calls to customer support. Faster delivery times mean happy, repeat buyers. Engaged team members means better customer outreach. It’s all interconnected, and it’s all worth it.
Improving and Innovating for the Long-term
In the world of business, complacency simply won’t cut it. To stay competitive, grow in your industry, and delight customers, you must constantly be on the lookout for ways to do things better than before.
The benefits of continuous improvements are vast, and they’re available to any company willing to invest in this important initiative. Our ERP consultants can help you get started. Contact us below to learn how to build a continuous improvement culture.