Before you select new enterprise software, like an ERP or SCM system, it’s important to ensure your goals are clear and your processes are optimized.
In other words, if you want to use technology to optimize your supply chain, you must ensure your processes align with this aim. This especially applies to your logistics processes.
The first step to improving your logistics processes is clearly defining your logistics strategy. Today, I’m sharing how to define this strategy so you can make the best use of your new software solution.
2025 Top 10 Manufacturing ERP Systems Report
Are you a mid- to large-sized manufacturing firm? This report is for you. Download it now to learn what kind of advanced functionality is available in the market today.
What is a Logistics Strategy?
Logistics is how resources are acquired, stored, and transported to their destination. A logistics strategy is the set of business processes, principles, and methodologies that guides your supply chain coordination. In my view, this strategy is about balancing cost and effort versus control.
Many organizations consider the realm of logistics to be its own separate entity and not a critical part of the company’s overall corporate strategy. However, in reality, logistics is integral to every part of an organization.
In fact, with the right supply chain logistics in place, companies can save money, improve output, and even optimize sustainability.
This is possible because a clearly-defined logistics strategy makes your organization more agile and adaptable. When you know exactly what’s going on, you’re able to adapt more quickly to changes that occur within your supply chain. You can identify a change before it occurs, anticipate the impact, and make necessary changes to ensure it doesn’t impact your level of service.
Reducing Costs Without Sacrificing Quality
I was involved in a scenario where the corporate transportation team was tasked with developing a logistics strategy to reduce costs where possible. The team had been using dedicated trucks from the distribution center that made multiple stops throughout a region, but this strategy was altered when the team found a new provider that offered significant savings on what seemed like equivalent service.
It turned out that the new service was LTL (less than truckload) service. Our freight was taken to a terminal and put on regional loads, as this made the most sense to the trucking company.
However, the unloading and reloading damaged some of the inventory, rendering it useless. This caused lost sales and reduced confidence from our customers.
While this first strategic move was unsuccessful, the organization eventually collaborated to develop a new strategy. The transportation team, operations team, freight provider, and competing providers convened to determine a solution that was less costly than the original trucking plan but less risky than the current plan.
As a result, the organization established a different outsourcing strategy. The plan was to still use a trucking company for freight but to control it more tightly. In this scenario, weekly dedicated trucks left the distribution center delivering product to field service branches across many states. While these controls added cost to our logistics operations, it allowed us to maintain the integrity of products and prevent damage.
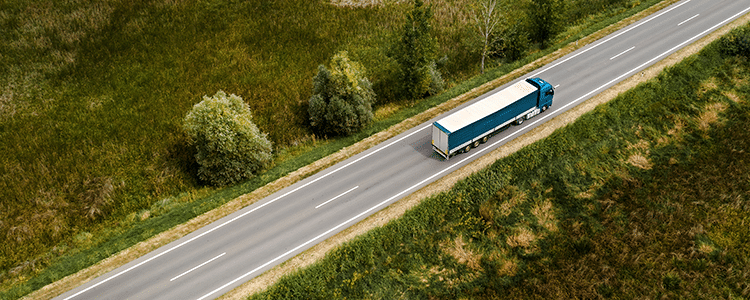
The 4 Pillars of a Logistics Strategy
While each company is different, the ideal strategy revolves around four basic pillars: strategy, structure, function, and implementation.
1. Strategy
This realm focuses on how to optimize logistics processes, so they align with and support the greater business goals.
Business leaders should clearly understand their company’s overarching objectives and how those relate to supply chain decisions. If there isn’t strong alignment here, then the other three pillars can’t fall into place.
2. Structure
Structurally, what facilities do you need to have in place to ensure a fully functioning supply chain?
This pillar considers the number of warehouses, distribution centers, and other resources required to optimize operations.
It also takes geographic location into account. Logistics executives should consider the potential cost savings and performance improvements of producing a product at one plant over another.
3. Function
It’s possible to have the right functions in place, but none are working as they should. Functionality should be built into every logistics strategy to ensure that assets are not only in place but are performing at top capacity.
4. Implementation
Designing a logistics strategy is a great first step, but it needs to be implemented across the entire organization to be effective.
Implementation refers to the process of communicating and deploying key strategic updates, such as new policies, procedures, and technology.
During this time, organizational change management is required to equip employees to use new technologies as they’re implemented.
5 Components to Consider When Developing a Logistics Strategy
1. Logistics Systems
If an organization already has logistics systems in place, it’s important to analyze their performance. Do they generate enough data to inform a logistics strategy?
If not, the organization may want to invest in new systems that can support its strategy both now and in the future. This could be ERP software, a supply chain management system, or another type of enterprise software.
2. Information
Speaking of data, is the information that drives your logistics systems accurate? Do you receive it in real time and is it up-to-date?
If an organization is using data to make supply chain decisions, it must be clean and correct in every instance.
In addition to facilitating day-to-day functions, this data can also be used to prove that a new logistics strategy is working.
How much did you ship on every load? Did the truck show up on time to load and unload? Was the freight damaged? What other costs were incurred?
I recommend tracking this information in an ERP system, so you can quantify business benefits and refine the system to remove excess costs or delays.
3. Outsourcing
Logistics activities can strain internal resources, which could impact service levels. A third-party logistics company can help offset this burden and free up employees to focus on mission-critical work.
Another reason to consider relinquishing some controls on logistics is cost reduction.
For example, an organization could outsource its transportation to a company specializing in truck freight. This can save time, money, and energy.
However, beware of the risks. My story earlier in the post proves that careful management of the freight provider is essential. Instead of just asking the provider for a rate and letting them figure out the best way to handle inventory, I recommend establishing clear guidelines for them to follow.
4. Competitors
An organization should know what their competitors are doing. If a competitor’s customer service levels continuously outpace its own customer service, the organization should investigate what they’re doing differently and what that would look like at their own organization.
5. Company Strategy
As an organization sets new objectives, it should make sure they align with the strategies already in place at the company. Misalignment could negatively impact the entire supply chain.
Optimize Your Logistics Strategy
In today’s world, it takes increased effort to ensure that products arrive at their destination in the manner the customer is expecting them, or at least in an acceptable manner. This is why developing a logistics strategy and selecting the right enterprise software is essential.
A clearly-defined logistics strategy supported by a robust software solution can keep your service levels high and your customers happy, even as changes occur throughout your supply chain.
Our team of enterprise software consultants can help you fine-tune your logistics strategy before software selection. Contact us below for a free consultation.