Are you managing an operational restructure for a struggling company in your portfolio? If so, you’re probably taking a closer look at ways to cut spending and maximize efficiencies across the enterprise, including the company’s supply chain.
An inefficient supply chain can do more than frustrate customers. It can also cost companies millions of dollars in lost revenue and non-productive labor. That said, supply chain cost reduction is a critical part of operational restructuring.
Today, we’re sharing how to use supply chain cost reduction to help a struggling company maximize every dollar it makes.
10 Tips for Supply Chain Cost Reduction
1. Make Better Use of Space
Regardless of the company’s size, there are significant costs associated with storing inventory and supplies in a warehouse.
We recommend performing an audit to determine if there are any instances of wasted or underutilized space. Is the available square footage in line with the company’s needs, or could it save money by relocating this effort into a space that’s more appropriate?
Achieving Operational Efficiencies
Our operational restructuring team can help you enable rapid change to achieve improvements in cash flow, working capital and profitability.
2. Automate Processes in the Warehouse
According to a recent report of more than 1,000 warehouse workers, nearly 40% said they were already using some form of robotics and automation.
If a company’s warehouse still relies on manual efforts to perform a majority of the work, automation can help save both time and money. In fact, automating core processes can deliver significant supply chain efficiencies.
A business process reengineering consultant can assess your portfolio company’s current operations to determine where automation technology could prove beneficial.
3. Streamline Ordering Process
How efficient is the company’s current ordering processes? What about its approval processes?
Implementing an ERP system can help streamline operations and improve visibility, ensuring all employees are relying on the same data. Otherwise, disparate systems can increase the risk of issues like duplicate orders, heaping unnecessary costs onto the company.
To learn more about ERP, check out our blog post, What is ERP in Supply Chain Management?
4. Monitor Customer Demand
Is your portfolio company spending time and money creating products that aren’t as in demand as they once were? Are there certain seasons during which some items are hotter than others?
We recommend developing a supply chain strategy that accommodates these fluctuations. This way, you can scale ordering and production up or down as required to save money.
5. Outsource When Necessary
Outsourcing remains one of the most common and effective supply chain cost reduction techniques. While adding service providers to the roster can add more out-of-pocket expenses, these costs may be less than what the company is already spending.
If the productivity and efficiency benefits that these providers deliver outweigh the extra financial burden, outsourcing can realign a struggling supply chain and lead to cost savings.
6. Listen to Customer Needs
It’s easy to get caught in the lightning-quick pace of technological innovation and invest in everything shiny and new. While it’s important to keep up with the competition, every innovation may not be right for every company because each company has unique customer needs.
By listening to customer needs, you can prioritize your technology investments and start with those that bring the most immediate benefits and highest ROI.
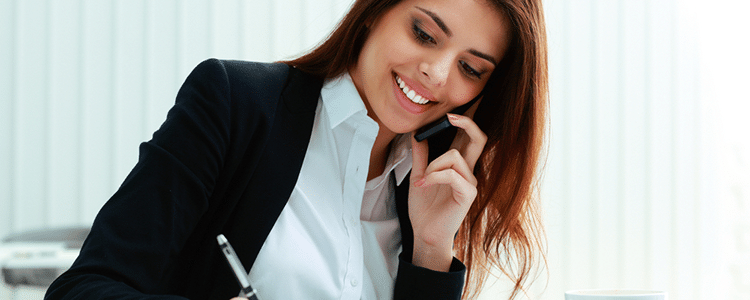
7. Focus on S&OP Before Implementing New Technology
Sales and operations planning (S&OP) should take place prior to implementing new technology.
This monthly, integrated management process helps executives focus on key facets of their supply chain, including sales and marketing, inventory management, demand management and more.
Ultimately, S&OP helps executives better understand the financial and business impacts of each process within the supply chain.
We recommend working with your portfolio company to understand and improve its supply chain processes, so you can determine what technology makes the most sense for the company’s desired future state.
8. Improve Data Insights to Increase Efficiencies
Supply chains are rich with data at every touchpoint, so many business leaders are implementing modern technology that collects and analyzes this data to produce helpful insights. Not only can these insights improve logistics and supply chain operations, they can also prove valuable to other business units, from marketing and sales to production.
Modern ERP software typically has advanced business intelligence powered by IoT that can help companies obtain insights, such as predictive maintenance, that lead to efficiency and cost savings.
9. Optimize Asset Utilization
Is the company making the best use of its current assets, ranging from heavy-duty machinery to the workforce itself?
From employee training and process scheduling to equipment maintenance and safety, it’s vital to take a close look at how to best utilize the resources the company already has. This will enable the company to gain supply chain efficiencies and reduce waste.
For example, if you want to optimize the utilization of the company’s existing workforce, employing organizational change management can ensure that employees have the tools and knowledge to efficiently perform their jobs. This is especially important when new processes and technology enter the picture.
10. Update Forecasts and Strategies Continuously
As struggling companies undergo operational restructuring, they must maintain a continuous improvement culture. This way, if a better route is identified, the company can adopt it without major implications.
The COVID-19 pandemic has revealed that even the best-laid plans can take a different direction as the larger business environment ebbs and flows. In these turbulent times of supply chain disruption, it’s wise to continuously update forecasts and strategies and focus on long-term cost reduction.
Minimizing Supply Chain Costs
If you’re looking for expert support as you try to help a portfolio company experiencing business distress, our business turnaround consultants are ready to lend our support. We’re experienced in helping companies across various industries identify and implement supply chain efficiencies and restore profitability.
To learn more, request a free consultation below.