The world of inventory management is constantly changing. As the innovation continues, more and more enterprise software applications and capabilities enter the market, helping companies improve their warehouse processes.
One of these innovations is voice directed picking. Also known as voice-directed warehousing or speech-based picking, this technology uses voice prompts to help users identify picking locations and find the items they need. The solution is hands-free and paper-free and only requires simple, mobile headsets.
While this sounds promising, it isn’t right for every company. Today, we’re looking at the aspects to consider if you’re on the fence about implementing it.
2025 Top 10 Manufacturing ERP Systems Report
Are you a mid- to large-sized manufacturing firm? This report is for you. Download it now to learn what kind of advanced functionality is available in the market today.
How Does Voice Directed Picking Work?
With voice directed picking, users are given clear verbal commands through headsets. The industrial microphones inside the headsets are connected to a mobile device that each user carries. This mobile device runs the dedicated voice application.
The commands that workers receive help them navigate through their facility, taking them directly to the products they need to pick. Once they find and select those products, they can speak back into the headset confirming that the mission was successful.
Then, voice recognition software (leveraging speech recognition technology) interprets the message and decides to authenticate or reject the picking based on the data received.
This process continues at each picking location until the order is complete.
Throughout the process, workers’ hands and eyes are free. All they need to do is listen and respond. Without cumbersome clipboards or tablets, pickers can focus more intently on the task at hand.
Though this type of software is most commonly used in warehouses, it can also be used at other locations, such as:
- Distribution centers
- Retail stores
- eCommerce fulfillment centers
- Factory lines
Integration With WMS or ERP Software
Most voice directed picking applications are designed to seamlessly integrate with an organization’s existing warehouse management software (WMS) or enterprise resource planning (ERP) system.
This two-way integration allows the application to access key inventory data, including specific order information and details about picking area locations.
With this information, the voice system can organize and create new work assignments and individual employee tasks. Then, it can share those instructions with order pickers on the warehouse floor.
For instance, the system may access a batch that contains multiple orders. It can scan that data, notify employees, and direct them to pick the orders as required.
While some voice systems are robust enough to initiate these types of tasks on their own, most leverage WMS integration to organize work in that capacity.
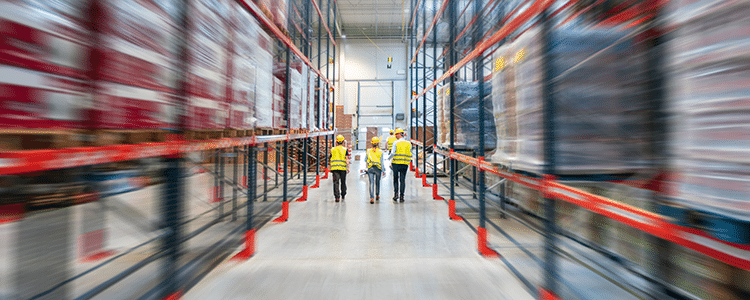
The Step-by-Step Picking Process
Now that we’ve covered the main points of voice picking software, let’s look at how this system works in a real-world scenario.
- The communication will begin with the WMS or ERP system.
- Once that system receives order preparation information, it will transfer that information to the mobile voice picking device.
- In turn, the device feeds the data to the headset.
- Once the worker hears the message, they can start traveling to where they need to go.
- When they arrive, they’ll know exactly where to turn and reach. This is because the voice in their headset clearly shares critical identifiers, including the SKUs and quantities to pick.
- Before picking, the worker will speak a control code back into the headset’s microphone to let the system know they found the right spot. Then, they will pick the merchandise as requested.
- Back at the WMS, the system receives confirmation that the picker found the right location.
- After the worker confirms the remaining quantity on the shelf, the WMS will update the inventory database to reflect the most recent numbers.
- If everything lines up, the system will mark that task as finished and proceed with the next task. However, if there’s any misalignment, the system will relay that information to the worker and will direct them on how to proceed.
- When the full order line has been picked, the voice system will let the worker know that the task is complete. Then, they’ll direct them on how to label, weigh, and properly pack each order.
Benefits of Voice Directed Picking (and a Few Concerns)
Voice picking technology can keep warehouse workers on task by simplifying the order picking process, which vastly improves productivity. This is true whether workers are picking full cases from pallets or using flow racks for individual piece picking.
In addition, training employees to use voice directed picking technology is relatively easy, so your workforce can be up and running in no time.
Another benefit is the reduction in user mistakes. The system knows exactly how much merchandise needs to be picked, and where it’s located. As a result, the margin of error decreases and time-consuming re-counts become a thing of the past.
Finally, voice directed picking software has the potential to improve warehouse safety. Workers can keep their minds, eyes, and hands on the task, without distractions that could sway their focus and put them at risk.
That said, this technology may not be an ideal fit for every type of warehouse or distribution center. This is especially the case with centers that mostly deal with full pallets of inventory.
In these facilities, full-pallet moves would require a great deal of travel if using voice-directed systems alone. For this reason, most of these providers choose to leverage more robust inventory management solutions, incorporating robot picking, RFID technology, and barcode scanning.
Then, there are sizing considerations to keep in mind. You should only implement voice picking software if your warehouse or distribution center meets these criteria:
- At least 50,000 square feet
- At least 300 SKUs
- At least 10 pickers per shift, working at the same time
Operations that fit this bill deal mostly with high volumes of product, including many mid-sized products. They’re big enough to necessitate voice picking but aren’t so large that they’ve gone fully to more advanced solutions, like robotics.
Implementing Voice Directed Picking at Your Organization
If you already have a WMS or ERP solution at your organization or you’re thinking about implementing one, then a voice directed picking system can be a great addition. This easy-to-learn technology can boost worker productivity, simplify inventory management, and even improve warehouse safety.
However, it’s important to make sure that your business model is a good fit before moving forward with this solution. Our team of enterprise software consultants can help you understand how the integration would work and the benefits it could deliver your organization. Contact us below for a free consultation.