Implementing a warehouse management system (WMS) or ERP system is a step in the right direction when it comes to warehouse automation. However, what if your current processes don’t fit the best practices in the new system? If this is the case, you need to understand what warehouse best practices are baked into the system and then improve your processes where it makes sense.
Haven’t selected a system yet? This post will give you an idea of some of the most common warehouse best practices you’ll find in a modern WMS or ERP system. This way, you can get a head start on thinking about process improvement.
Why are Warehouse Best Practices Important?
Best practices exist for a reason. They’re designed to help companies navigate some of the most common challenges in their niche.
In the manufacturing industry, most of these best practices center around operational logistics. A few of the key issues facing supply chain leaders today include:
- Ensuring safe and secure manual handling
- Hiring and retaining skilled laborers
- Implementing IoT technologies
- Embracing robotics and automation to anticipate demand
- Maintaining accurate inventory levels
- Meeting customer expectations for shipping and delivery
For all these concerns (and more), many WMS and ERP systems provide preconfigured best practices that can help alleviate your pain points.
2025 Top 10 Manufacturing ERP Systems Report
Are you a mid- to large-sized manufacturing firm? This report is for you. Download it now to learn what kind of advanced functionality is available in the market today.
5 Examples of Warehouse Best Practices
1. Smarter Slotting
Efficient SKU retrieval is essential to optimizing time in your warehouse. Most ERP software will include slotting functions that help you decide where items are stored, as well as the distance that employees will need to travel to get them.
Depending on your setup, there are a few different ways you can approach this task. Some companies choose to slot their items by velocity, where the highest-volume items are located closest to the shipping dock for quick acquisition. Others choose to slot simply by fit because they want to maximize the amount of cubic space available in their warehouse. Companies that use bulk picking, on the other hand, may decide to place high-volume, small items close to their shipping dock.
With any technique you choose, it’s critical to match your slot sizes to the products they contain. Ensuring that each pick slot is appropriately sized to handle the size and sales of the items inside enables you to maximize your use of each cube.
The slotting best practices within your ERP system are likely optimized for this task, allowing you to analyze each SKU to ensure it’s delivered in the most efficient fashion.
2. Detail-rich Receiving
Gone are the days when manual receiving was enough to capture all relevant product data. Now, you can find WMS and ERP systems that handle this step for you, inputting the key details you need to know, including product style and quantity.
As the system scans each incoming barcode, it can print a new label in seconds, each containing valuable information such as SKU, vendor name and order number. From there, your system can also assign each item to the correct, corresponding storage location based on its characteristics.
We recommend working with your suppliers to ensure they’re providing as much data as possible to leverage these helpful features.
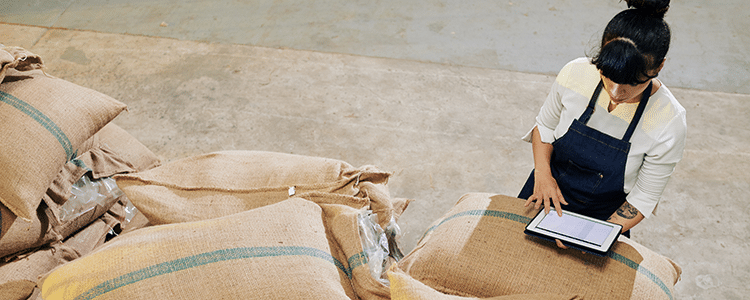
3. Concise Cycle Counting
Cycle counting is a necessary, albeit tedious part of warehouse maintenance and management. However, an ERP system with pre-configured best practices can help automate and expedite this process, keeping your stockroom in optimal working order without any of the stress.
You’ll start by defining the frequency that you want your cycle counts to follow. Some companies choose to perform this task daily, while others prefer weekly or another pre-defined pattern. From there, you can narrow your preferences by item type for an even more focused approach.
For instance, you can choose to count high-cost or high-volume items more frequently, as these can’t be replaced easily or on short notice. This approach maximizes employee productivity and reduces downtime as they search for lost items. When you have real-time count updates always accessible, you can analyze them on-the-go and make more informed business decisions.
4. More Strategic Picking
Many WMS and ERP systems are preconfigured with strategic picking approaches. There are a few different strategies you can take when designing your picking approach, including fixed-location, batch, zone and wave picking.
Ultimately, the strategy you employ will depend on several factors, such as the number of different SKUs you have. In this instance, companies with complex shipping systems and many different SKUs can benefit from wave picking, which combines elements of zone and batch picking.
5. Optimized Warehouse Space
Do you know how much used or unused space you currently have, across all your different warehouse zones? Leaving space unoccupied could limit your production.
Modern WMS systems integrate with barcode scanners and bin location trackers to help you quickly identify and track unoccupied warehouse areas. These insights can help you more accurately measure your current capacity and space availability.
For example, you may find that you have room available to perform kitting and subassembly, where employees can perform light packaging activities before shipment. You can configure these spaces directly in your system, so material handlers know how and where to deliver the items.
As you optimize available warehouse space, you can also keep track of how that space is being used. Integrated labor management tools help you keep an eye on employee efficiency and performance.
Discover More Warehouse Best Practices
Transitioning your warehouse operations onto a modern, automated platform can revolutionize the way your company receives, handles and delivers its core products.
As you prepare to implement a WMS or ERP system, it’s important to improve your processes to fit the best practices within the system. This will help you avoid costly and time-consuming software customization.
Process improvement is just one implementation success factor to keep in mind. Be sure to check out our WMS implementation checklist for a more complete list of success factors.
Whether you’re interested in ERP selection, ERP implementation or business process reengineering, we can help. Request a free consultation below.